Hot Crimping for Joining Magnet Wires, 2012-04-02, Assembly Magazine
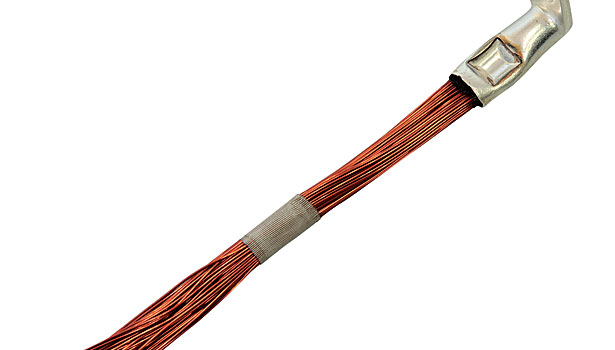
Using new and innovative technology can be risky, but it can often be rewarding. European electric-motor manufacturers Bosch, Siemens and Volkswagen realized this in 2011 after discovering hot crimping. For decades, these companies used machines or chemicals to strip the enamel coating off the ends of magnet wires before crimping them to copper ring terminals or sleeves. Hot crimping, in contrast, vaporizes the insulation during crimping of the wire and terminal or sleeve. By eliminating the stripping step, hot crimping enables manufacturers to increase productivity. . . .
Hot crimping technology features specially designed welding heads that quickly attach terminals to wire from 30 AWG to 350 MCM.

Hot Crimping for Joining Magnet Wires, 2012-04-02
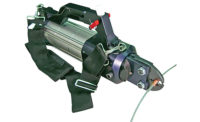
Hot Crimping for Joining Magnet Wires, 2012-04-02

US11088002B2 - Substrate rack and a substrate processing system

Hot Crimping for Joining Magnet Wires, 2012-04-02

US11015245B2 - Gas-phase reactor and system having exhaust plenum

US11031242B2 - Methods for depositing a boron doped silicon

US20190125475A1 - Positive shaft rotation lock activated by jaw

Hot Crimping for Joining Magnet Wires, 2012-04-02

USD947913S1 - Susceptor shaft - Google Patents

US20190125475A1 - Positive shaft rotation lock activated by jaw

RU2701349C2 - Кассета с крепежными элементами для создания гибкого
Material: Thickened red copper, with high load capacity, strong conductivity, low resistance, low temperature, stability, surface pickling, not easy

10Pcs U Shaped Thick Copper Crimping Terminal Connector Kit, Copper Crimping Sleeve, Non Insulated Copper Wire and Wire Connection Terminals, Suitable

BEKMLOD 10Pcs U Shaped Thick Copper Crimping Terminal Connector